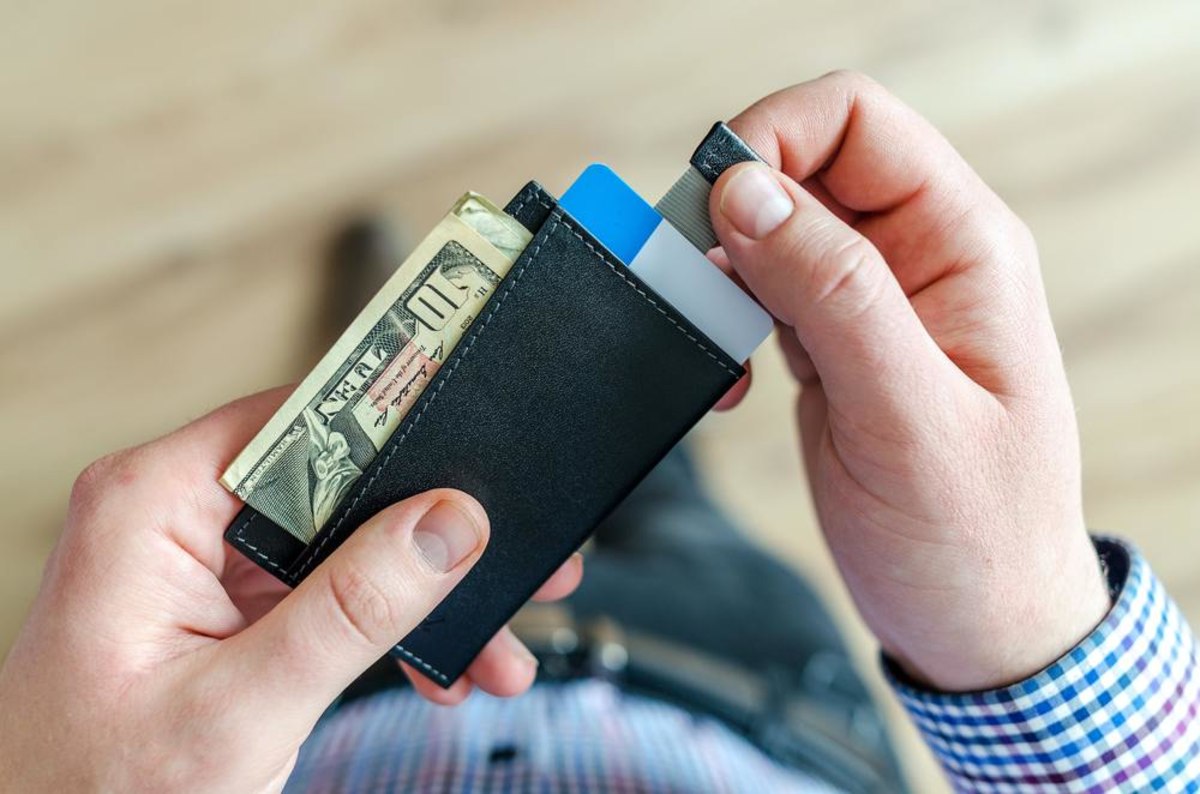
Dirt Is Costly
by Transport Topics Online
November 20, 2019
In times like these when the economy and budgets are tight, often one of the first steps toward cutting costs is reducing or eliminating equipment-washing programs. There are important factors to contemplate before doing that.
For example, soil and debris buildup on mechanical components insulates heat-sensitive components and shortens their life; promotes electrical shorts and vehicle fires; creates acids that erode finishes, base materials and electric components; accelerates wear and abrasion and shortens lubrication life.
Effects on your equipments’ paint and metal finish may include a breakdown in the chemical structure of paint surfaces, reducing paint life; promote scratches and scuffing because of the abrasive effect; and require more frequent refinishing — potentially doubling the price.
Cutting back on or reducing equipment washing also encourages more frequent Department of Transportation inspections — which can impede timely deliveries, reduces your employees’ pride in workmanship, means assigned tasks require additional time, promotes dirt and dust contamination of equipment, and reduces the ability to effectively diagnose mechanical issues. It also creates higher maintenance costs, discourages third-party repair facilities from working on your fleet, affects the quality of preventive maintenance inspections, and affects your ability to hire competent drivers and technicians.
And that’s just within your shop. Your customers’ perception of you also can change to a poor one, since your fleet is your billboard and primary form of advertising. It can even have a negative effect on your negotiating ability, mean poor overall perception of your fleet in the community and have a negative effect on pricing.
Dirty equipment can affect your ability to recruit good drivers, imparting an “I don’t care” attitude throughout the driver ranks. It can foster an unsafe working environment, reduce
the quality of communication between operations and maintenance, and create additional employee turnover.
All this can reduce the value of your assets — reducing return on capital — causing negative vehicle residual value — affecting customer confidence and contributing to a higher variable cost structure.
Finally, dirty equipment has an effect on safety. Why?
• Dirty light fixtures provide less headlight range and tail/brake/running light brightness. Less headlight range, even a few percent less, means it’s harder to see road debris and other conditions. The resulting tire damage and suspension wear mean a slightly higher accident risk.
• Dirty windshields lessen the ability to see and react to road conditions, and there’s more glass wear when wipers are used to clear the dirt, leading to wiper burn and distorted views.
• Dirt and grease buildup on steps, frame rails and grab handles increase the chances of slip-and-fall accidents.
• Dirt and grease buildups also can interfere with proper operation of hitches and doors, leading to accidents and injuries.
Can you put a quantifiable figure on what it costs if you do not have an effective equipment wash program? The answer is “yes.” Taking into account what a fleet wash program will cost the organization, not having one will increase your equipment costs a minimum of 25%. The key is to have such a program and manage as you do other aspects of the business.
Michael Buck
President, MCG Fleet Management Consulting
St. Simons, Ga.
Credit: Transport Topics Online